Ensuring Workplace Safety: Safety Audits
Words: Michael Rosser
Words and Photos: Michael Rosser, President, Corporate Safety Services
Audits play an extremely important role in an accident prevention program. A safety audit, or as some call it, a safety inspection, is a tool that is used for evaluating just how effective your safety program really is. I believe safety audits are also a way to measure the overall safety culture of your company.
First, let’s discuss whether safety audits are required or not. The Occupational Safety and Health (OSHA) standards are quite clear on conducting safety audits:
29 CFR 1926.20(b)(1)
It shall be the responsibility of the employer to initiate and maintain such programs as may be necessary to comply with this part.
29 CFR 1926.20(b)(2)
Such programs shall provide for frequent and regular inspections of the job sites, materials, and equipment to be made by competent persons designated by the employers.
Paragraph (b)(1) tells us that employers must have any program necessary to comply with the standards, such as Fall Protection, Respiratory Protection, Confined Spaces, Scaffolding, etc.
Paragraph (b)(2) tells us that those programs must include provisions for frequent and regular inspections.
As a safety consultant, I am frequently at one of our local OSHA offices conducting an Informal Conference once an employer has received citations. And for many years now, one of the first questions that OSHA asks is if the employer has documentation to show that safety inspections are being performed on their job sites and facilities.
So, we’ve determined that we must be conducting safety audits of our job sites, facilities, employees and equipment. Now, let’s discuss who should be doing those audits.
First and foremost, your superintendent or foreman should be conducting safety audits on a regular basis. My recommendation is at least weekly. If your company has either a full-time safety manager or an additional-duty safety coordinator, they should be completing safety audits several times a month at each location. And, if your company has a safety committee, its members should also be performing safety audits on a regular basis. But what about other company personnel that visits your job sites? Do project managers ever go to the job sites? Does the company owner or president visit the projects? If so, they should also be conducting a safety audit every time they’re on site (maybe in a different article, we’ll discuss why those people should also be trained in the OSHA safety requirements). Does it have to be in as much detail as when the safety manager does one? No, but it should still be documented as such by either a written report or even an email stating an audit was conducted. The key point here is documentation. As we’ve learned over the years from OSHA, “If it isn’t documented, then it didn’t happen.”
So far, we’ve determined that safety audits are required, and we’ve discussed who should be doing them. Now let’s talk about how we should conduct the audit. Over time I’ve learned that using a checklist is invaluable when doing an audit. You probably already use one to make sure each new hire completes all the necessary paperwork during the onboarding process. Or you have a checklist that your scaffold competent person uses to inspect the scaffolding each morning.
When Corporate Safety Services started in 1987, we used a three-part, carbonless paper form on a clipboard when doing audits. We left one copy at the job site, faxed a copy to their office and kept at least one copy in their client file at our office. I still have that form here on my computer, and if that’s the way you want to document your audits, then absolutely do so.
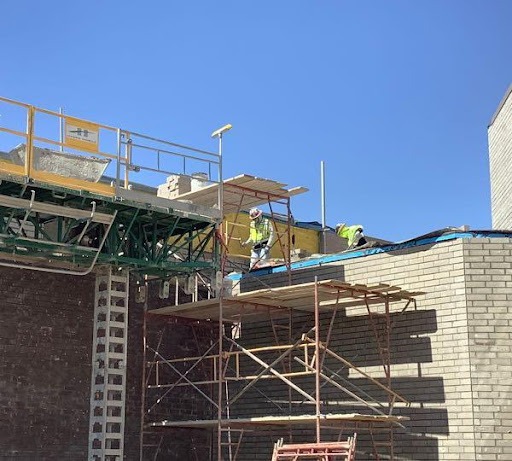
However, as technology has advanced, so have different ways to document audits. Over the last 15 years or so, we’ve used several different apps on our cell phones or iPads to document our audits. We average about 40-50 audits a week for our clients, and using these apps makes it much easier to track findings and corrective actions as well as get the reports to the people that need to see them almost immediately after finishing the audit. I’m not here selling software, but most of the major providers of auditing apps have a version that lets you do 5-20 audits a month for free. Have your foremen try different apps for a month or so and see which one they’re comfortable using.
Ok, let’s get to our next topic. What should we be looking for when conducting a safety audit? When I conduct an audit for one of our masonry clients, it starts the moment I get out of my truck. As I’m putting on my safety helmet and reflective vest, I’m looking at the overall impression I get from the entire project. What does housekeeping look like? Do other subcontractors appear to be working safely? Does it appear the general contractor is enforcing the safety rules on the site?
After checking in with the general contractor (I highly recommend this if you aren’t on the project on a regular basis. General contractors can get a little touchy when they see strangers walking around the project), I go find the foreman for our client.
Is there a particular order of the things I want to look at? No, not really. Remember, the audit needs to be thorough. We should be looking at equipment, employees and documentation.
If scaffolding is involved, I want the scaffold competent person walking with me so they can explain anything I have questions about. In this article, I’m not going to tell you exactly what to look for when inspecting a scaffold. Your competent person should know as much, or more than I do, about the scaffolding you’re using. After I’m done looking at the scaffolding, I look at other equipment on the site. Forklifts and mixing stations are good examples. Is the forklift operator wearing their seatbelt? When I ask questions about doing the daily inspection of the forklift and about the load they’re carrying, they should be able to answer them.
Then I want to talk with the employees. While talking, I can see things like personal protective equipment (PPE), tools and work practices. I try to ask employees questions that I’ve seen OSHA ask during employee interviews. What kind of safety training have you had since being hired? Was that training in a language that you understood? Does the foreman hold a toolbox safety meeting every week?
Finally, I talk with the foreman for a few minutes. Where is this week’s toolbox talk paperwork? Do your forklift operators have current certifications? Have you had any injuries, mishaps or near-misses on this project? Remember, while conducting the audit, you should also provide any safety help or assistance needed.
Now you’ve completed the audit. Now it has to be documented.
Another suggestion for everyone. When we arrive at the job site, we have the foreman select an employee who walks with us and learns what we’re looking for during our safety audit. It’s a great educational opportunity, and before long, every employee is doing a safety audit every day at work.
If you’d like the paper audit form or recommendations on an audit app, just drop me an email at mike@corporatesafetyservices.com