Masonry Advantages
Words: Steven Judd
Words and Photos: Steven Judd, Technical Director of Interstate Brick
Vitruvius, an ancient Roman Architect and Engineer, coined a phrase of three attributes intended to be applied to the ideal material or form: Firmitas, Utilitas, Venustas. These three attributes are idea to apply to discussions of masonry: Strength, Utility (usefulness), Beauty.
Clay (or shale) brick masonry has been used for thousands of years (as far back as 9,000 years ago) for many obvious reasons: it can be made practically anywhere; it uses readily available raw materials; when fired, it has extreme durability and resistance to extreme weather; it carries very heavy loads; it is fire-proof; it can be reinforced to resist high tensile forces; it can be made in various sizes and shapes and can be combined in various ways and orientations to create unlimited forms; it is colorfast; and, it is beautiful. Not many construction materials can say all those things.
For the discussion herein we will discuss masonry in terms of two main genres, veneers, and reinforced structural elements, primarily, but not exclusively, made of brick made from fired clay and shale. There are other genres, like embedded thin brick in precast, and hand-set thin brick over multiple substrates, but, alas, will save discussion of those for another article.
Veneers
Brick veneer (or concrete veneer units), generally 3 inch to 4 inch thick, placed on the outside of a building, enclosing an airspace, usually 1” to 2” deep, anchored back to the substrate wall system. The masonry veneer wall system may include exterior insulation and should always include flashings and air/water-resistant/vapor barriers. This wall system is considered the “perfect wall”. It provides a non-combustible and durable weather barrier. The encapsulated air gap, whether the air space is vented or ventilated, provides enhanced thermal performance [proven via BIA funded testing at the National Brick Research Center]. The weeps and/or vents used in this system provide a path to eliminate water that may infiltrate past the face of the veneer (barrier surface) due to gaps in sealants, leaky seams in flashings and copings, bee-holes in the mortar, cracks due to building movement, and other anomalies. Water is easily drained, and consequently, it is extremely rare that water penetrates into the interior space. This wall system has proven functionality and is exceptionally useful in harsh environments and is particularly advantageous for the wildland-urban interface (WUI), where fires are a major concern. Additionally, brick veneer, up to a point, will resist light, low velocity, projectile impacts and low energy (pistol) ballistic impacts, providing enhanced safety for building occupants.
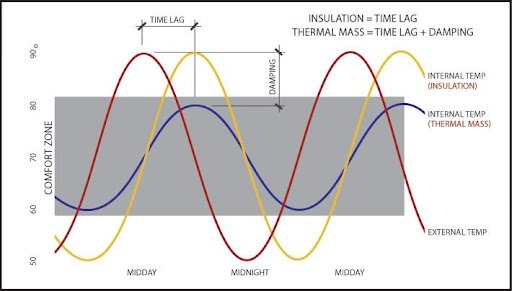
Most 4” (nominal) thick brick walls can qualify as a “mass wall”, based on their calculated heat capacity, which can reduce the requirement for excessive amounts of insulation in the exterior walls, as compared to other wall assembly systems. The “mass wall” effect reduces energy demand and reduces the cost of construction as well as reduces ongoing operating costs for temperature control. Mass walls have two distinct energy advantages: 1) they act as capacitors and take time to heat up and cool off, introducing a time lag, of shifting the peak temperatures to later in the day, potentially to off-peak hours, and 2) mass walls have insulating properties which act as dampeners, reducing the heating and cooling demand on the substrate wall and interior space. ASHRAE 90.1 recognizes the benefits of mass walls by reducing the required insulation for mass walls, as compared to other wall systems, for the various climate zones.
The compressive strength of fired brick generally has sufficient capacity to support brick veneer stacked over a mile high, although codes would not allow that. Veneer can carry significant loads. The code limits continuous veneer installations over wood or steel stud framing to a height of 30 feet (or 38-feet and a gable), not because of the limitation of the brick, but due to accommodation of the differential movement between the veneer and the backing materials. All materials, including veneers, expand and contract due to thermal gradients; day-to-day; day-to-night; season to season; year to year, and the wall assembly materials have irreversible volumetric changes: brick expands, concrete shrinks, and wood shrinks.
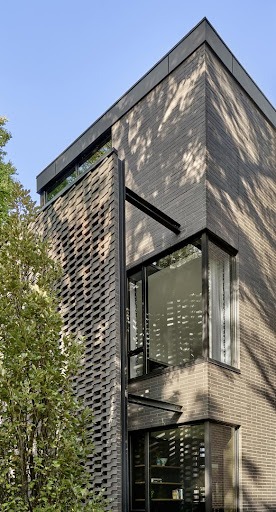
Veneer brick can be produced in many sizes and profiles and can be assembled to produce many different shapes and forms. Of particular design interest of late are perforated screen walls, such as the image to the right, which can require some special shapes to achieve the desired pattern of openings:
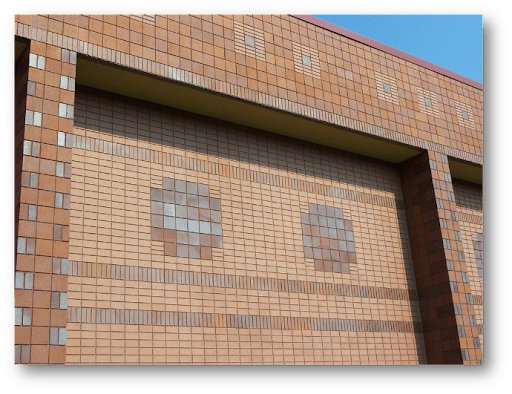
Lastly, large format masonry units can be used to replace modular masonry units. Although the costs of the larger units are higher than the smaller units, the savings in labor of setting fewer large units nearly guarantees a cost reduction of the wall, because the most expensive portion of the wall is labor, not material. Anything the reduces labor, like oversize units, reduces the overall cost of the wall. Special shapes can also reduce the cost of a wall. Think about setting 6 soldier-oriented brick (standing on end, narrow face visible), mudding and adjusting each one, as compared to setting one 8” tall x 16” long unit with 5-slots. The look is the same, but there is less lifting, less labor, less brick adjusting and less mortar being used. The four bands of soldier coursing in this image were made by using large format face brick - 8” tall x 16” wide units - with 5 extruded slots, tuck pointed with mortar.
Structural Masonry
Structural masonry encompasses a wide range of systems, including the typical load bearing and shear wall buildings, but also prefabricated (and sometimes pre-stressed) masonry walls, reinforced masonry curtain walls and veneers, reinforced arches, domes, vaults, and more.
The Excalibur Hotel in Las Vegas is one of the largest and tallest reinforced masonry (CMU) buildings built to date, standing with four hotel room towers that are 28-stories tall - the tallest reinforced masonry building constructed in a moderate seismic zone. The Little America Hotel in Salt Lake City, Utah, a 17-story building is one of the tallest Reinforced Hollow Clay Masonry (RHCM) buildings built to date, also in a moderately high seismic zone. Structural masonry can be designed to withstand extreme events. Mid-rise building heights are not a problem with structural masonry.
Just as brick veneers can be extremely useful in the wildland-urban interface for preservation of facilities, structural masonry can be a very effective fire separation material from building to building and from interior space to interior space. Structural masonry walls, when filled with appropriate non-combustible materials can achieve a 4-hour fire-resistance rating at an 8-inch wall thickness, and somewhat lower fire-resistive ratings for thinner walls. These fire-rated walls can be used as zero lot line structural walls, or interior dividing walls between stairs and occupied spaces, or between occupied spaces, such as apartment separation walls, which can be the support walls.
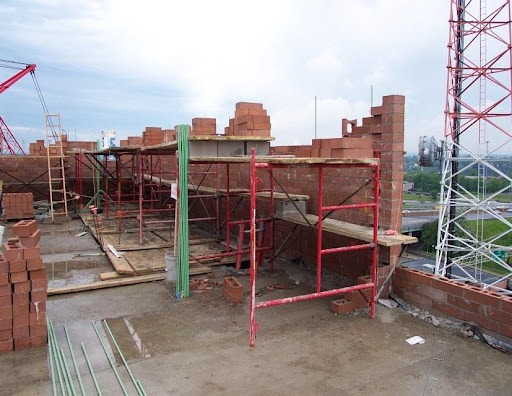
For tight lots, it is possible to construct structural load-bearing and shear walls from the inside of the building (inside-out construction), eliminating the need for exterior scaffolding to install brick veneer. This system is accomplished using a structural curtain wall system. The reinforced structural veneer walls are self-supporting, full height, and only tied back to the floors at discrete points for out-of-plane loads. For this system interior bearing and shear walls are constructed simultaneously with the exterior reinforced masonry enclosure wall working from the established floor plate. Once the exterior walls are placed to a level several courses above the next floor level, and the interior walls are placed up to the bearing elevation of the next upper floor, the next floor is erected, exterior walls are tied back, and the process of constructing the interior and exterior walls is repeated, level by level. Continuous interior rigid insulation can be applied and taped to create the A/W/V barrier, tied to through-wall flashing, and then light gauge framing (22- to 25-gauge steel studs) can be added for electrical distribution and interior finishes. The result is a building with a brick facade, without the need for scaffolding, without the need for the thousands of brick ties, and without the need for heavy gauge exterior wall steel stud framing. Construction cost is decreased, and construction speed is increased. This method has been used on over half a dozen buildings ranging in height from 12- to 17-stories, on various apartments and hotels.
Inside-out Construction
Single wythe structural brick can be used where two-wythe brick veneer over CMU is used on site structures, to match a building with brick veneer. Examples are: screen walls, trash enclosures, grade separation walls, planter walls, sports facilities, and signage. A two-wythe solution (brick veneer over CMU backup) can easily be changed to a single-wythe structural brick that is made to match the main facility brick veneer. The single wythe structural wall will always be less expensive than a two-wythe masonry wall system: less labor and less material.
There are many structural masonry manufacturers in the United States and Canada that generally have material available in stock. Some masonry manufacturers produce structural units on a ‘made-to-order’ basis, but others continually produce the units. Lead times vary from plant to plant, based on production scheduling protocols (similar to steel mill rolling schedules), so it is best to contact the supplier, but in general, lead times for masonry are much shorter that lead times for some structural steel elements. The world keeps changing, so it is prudent to check supply lines.
On several occasions last year, contractors in a particular upper Midwest area approached the local Masonry Institute to see if there was a solution for a construction system with shorter delivery times than the steel framed buildings that went out to bid. It was possible in several instances to redesign the buildings using structural masonry and complete the construction in shorter time and less money than the original project required for the structural steel system, even with the added time and cost for re-design. Structural steel was still utilized for roof framing, but the long lead items in steel were changed to load-bearing structural masonry.
Whether veneer or structural masonry, there is significantly more design flexibility using the small modular units of masonry than with other materials. Masonry offers many solutions to various design challenges. New holographic imaging systems and computer modeling have advanced to the point where a mason can set each individual brick to a pattern or layout sequence without story poles, or stringlines, where no two bricks align with any adjacent bricks, creating movement and patterns in masonry construction that were heretofore extremely difficult or impossible to create. Utilizing many sizes, almost unlimited shapes, and new installation means and methods, the possibilities for masonry design and construction are nearly limitless, providing the strength, utility, and beauty that is the essence of masonry.